{{i.title_en}}
Axial Piston Fixed Pump HD-A2FO
MOQ: 100 PCS
Note: If you have any questions,please contact us
- 1.Sizes 5~500 ,Series 6, Nominal pressure 400 bar, Maximum pressure 450 bar
- 2.Fixed pump with axial tapered piston rotary group of bent-axis design, for hydro-static drives in an open circuit.
- 3.For use in mobile and stationary applications,the flow is proportional to the drive speed and displacement.
- 4. The drive shaft bearings are designed for the bearing service life requirements usually encountered in these areas.
- 5. High power density,Small dimensions,High total efficiency,Economical design, One-piece tapered piston with piston rings for sealing
- HD-A2FO
BEIJING HUADE HYDRAULIC INDUSTRIAL GROUP CO.,LTD
Since:
1979
Product Description
HD-A2FO Axial Piston Fixed Pump Ordering Code
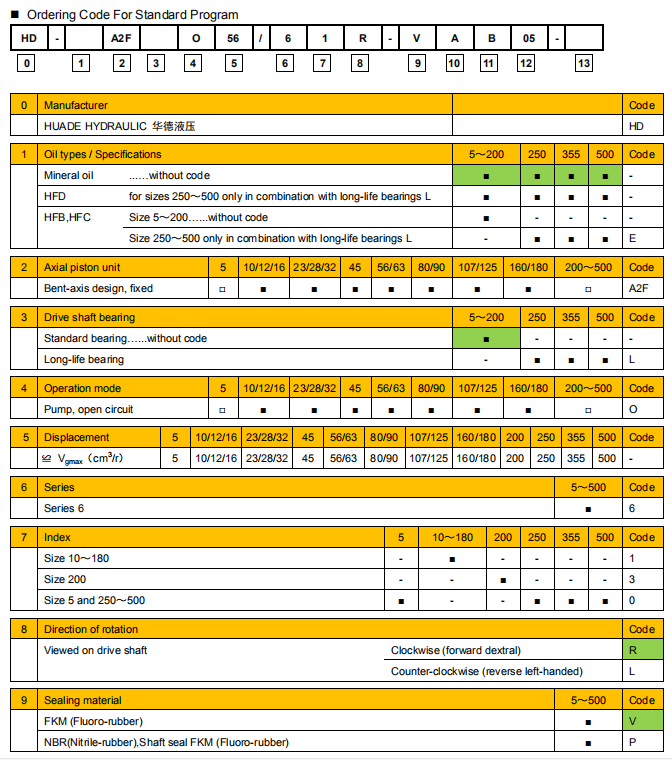

HD-A2FO Axial Piston Fixed Pump Technical Data
Shaft seal…Permissible pressure loading
p The service life of the shaft seal is influenced by the speed of the axial piston unit and the case drain pressure (case pressure).
p The mean differential pressure of 2 bar between the case and the ambient pressure may not be enduringly exceeded at normal operating temperature.
p For a higher differential pressure at reduced speed, see diagram.
Momentary pressure spikes (t < 0.1 s) of up to 10 bar are permitted. The service life of the shaft seal decreases with an increase in the frequency of pressure spikes.
p The case pressure must be equal to or higher than the ambient pressure.
n Static characteristic
p Sizes 10 to 200
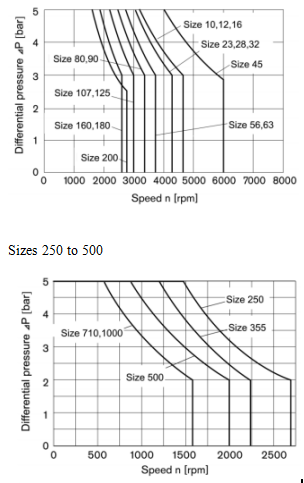
Temperature range
The FKM shaft seal may be used for case drain temperatures from -25 °C to +115 °C
For application cases below -25 °C, an NBR shaft seal is required (permissible temperature range: -40 °C to +90 °C). State NBR shaft seal in plain text when ordering. Please contact us .
Direction of flow
Direction of rotation, viewed on drive shaft
| Direction of flow
|
clockwise (R)
| S → B |
counter-clockwise (L)
| S → A
|
Long-life bearing
Sizes 250~500
For long service life and use with HF hydraulic fluids. Identical external dimensions as motor with standard bearings. Sub- sequent conversion to long-life bearings is possible.
Bearing and case flushing via port U is recommended .
Flushing flow...recommended
Sizes | 250 | 355 | 500 |
qv flush (l/min) | 10 | 16 | 16 |
Ports | Port for | Diagram |
A, B S T U(Sizes 250~500) | Working port Suction port Drain port Flushing port | ![]() |
Working pressure range
Working pressure range valid when using hydraulic fluids based on mineral oils
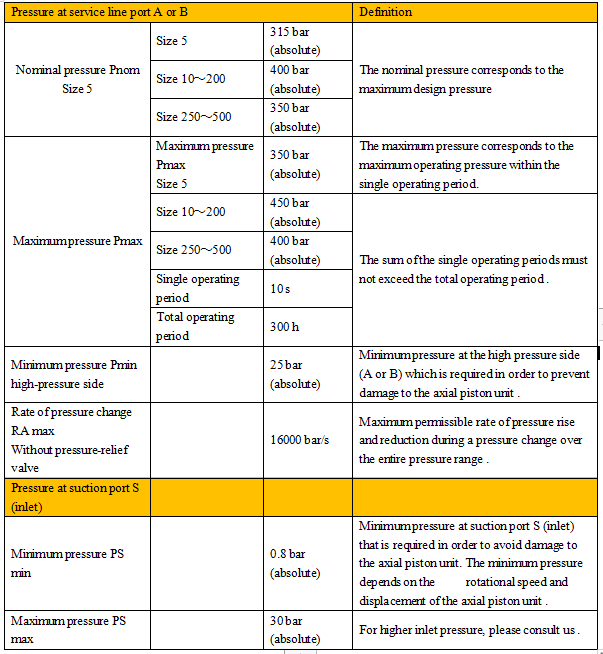
Note:Values for other hydraulic fluids, please contact us
Rate of pressure change RA max
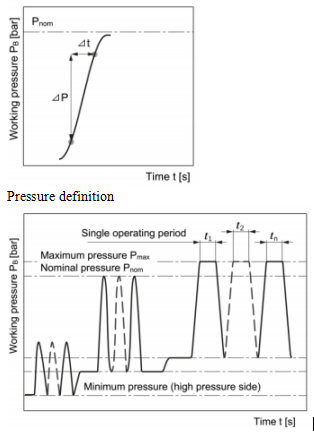
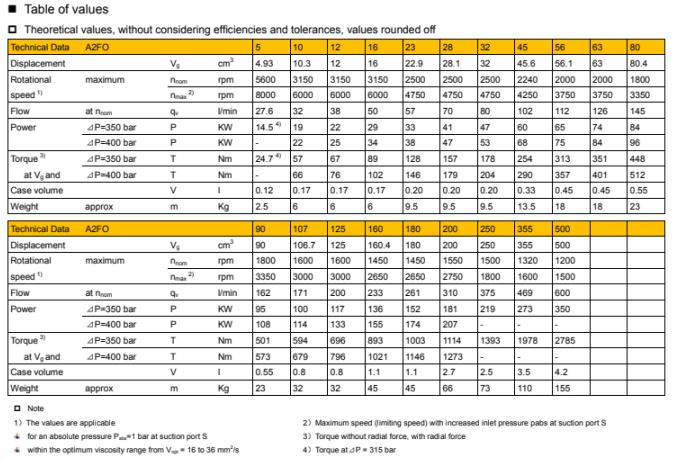
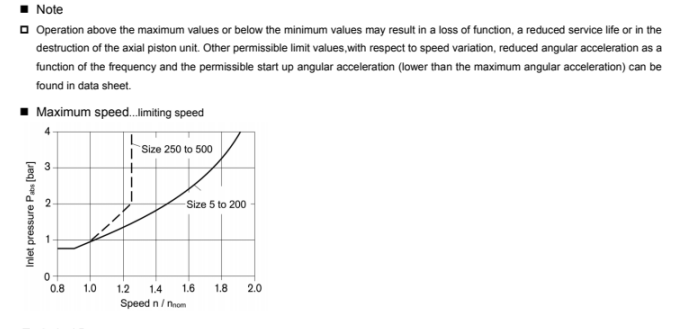
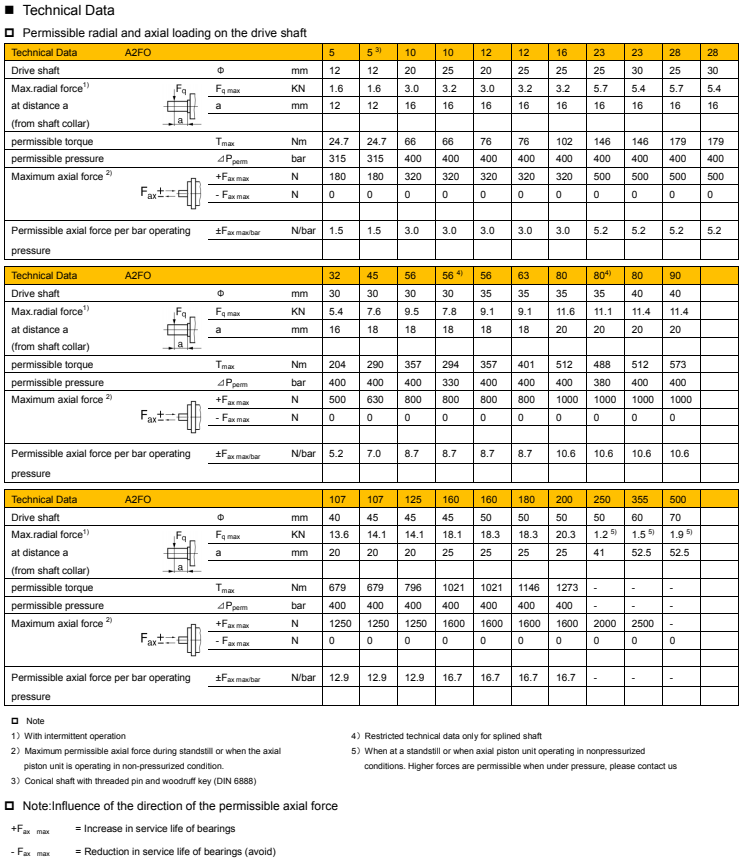
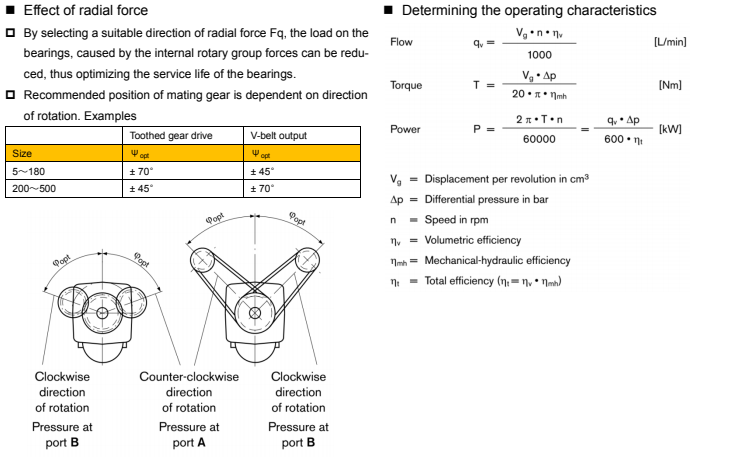
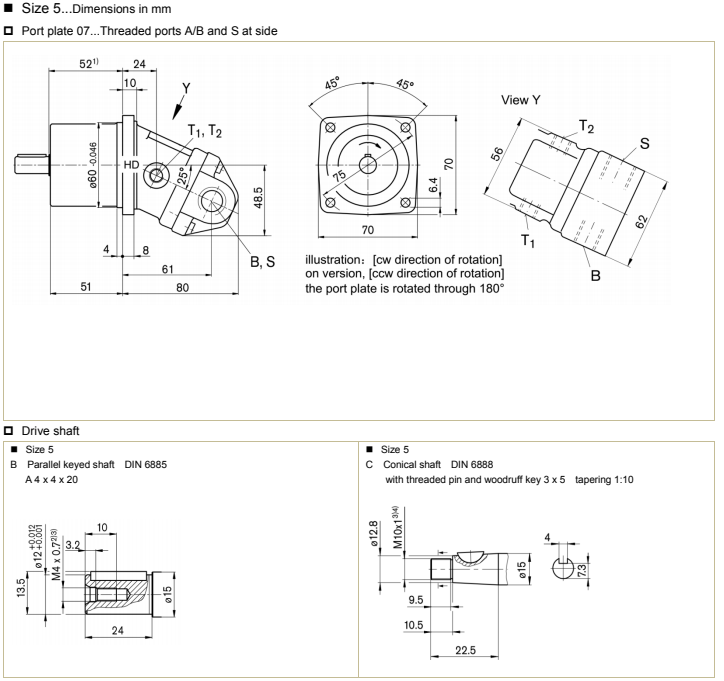
Ports
Ports | ![]() | Standard 6) | Size 3) | P Max [bar] 5) | State 8) |
B(A) | Working port | DIN 3852 | M18 x 1.5 deep 12 | 350 | O |
S | Suction port | DIN 3852 | M22 x 1.5 deep 14 | 30 | O |
T 1, T 2 | Drain port | DIN 3852 | M10 x 1 deep 8 | 3 | X/O 7) |
Note
1) To shaft colla 5) Momentary pressure spikes may occur depending on the application.
2) Center bore according to DIN 332 (thread according to DIN 13) Keep this in mind when selecting measuring devices and fittings.
3) For the maximum tightening torques the general instructions must be observed.
4) Thread according to DIN 3852, maximum tightening torque 30 Nm
5) Momentary pressure spikes may occur depending on the application.
6) The spot face can be deeper than specified in the appropriate standard
7) Depending on the installation position, T1 or T2 must be connected
8) O = Must be connected (plugged on delivery) X = plugged (in normal operation)
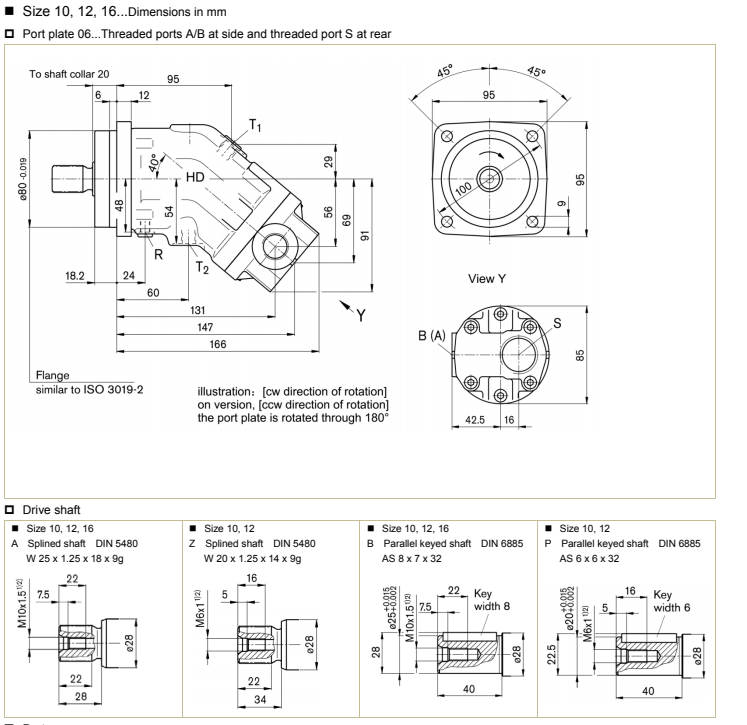
Port
Ports | Port for | Standard4) | Size 2) | P Max [bar] 3) | State 7) |
B(A) | Working port | DIN 3852 | M22 x 1.5 deep 14 | 350 | O |
S | Suction port | DIN 3852 | M33 x 2 deep 18 | 30 | O |
T 1, T 2 | Drain port | DIN 3852 | M12 x 1.5 deep 12 | 3 | X/O 6) |
R | Air bieed | DIN 3852 | M8 x 1 deep 8 | 3 | X |
Note
1) Center bore according to DIN 332 (thread according to DIN 13)
2) For the maximum tightening torques the general instructions must be observed.
3) Momentary pressure spikes may occur depending on the application.
4) The spot face can be deeper than specified in the appropriate standard
6) Depending on the installation position, T1 or T2 must be connected
Keep this in mind when selecting measuring devices and fittings.
7) O = Must be connected (plugged on delivery) X = plugged (in normal operation)
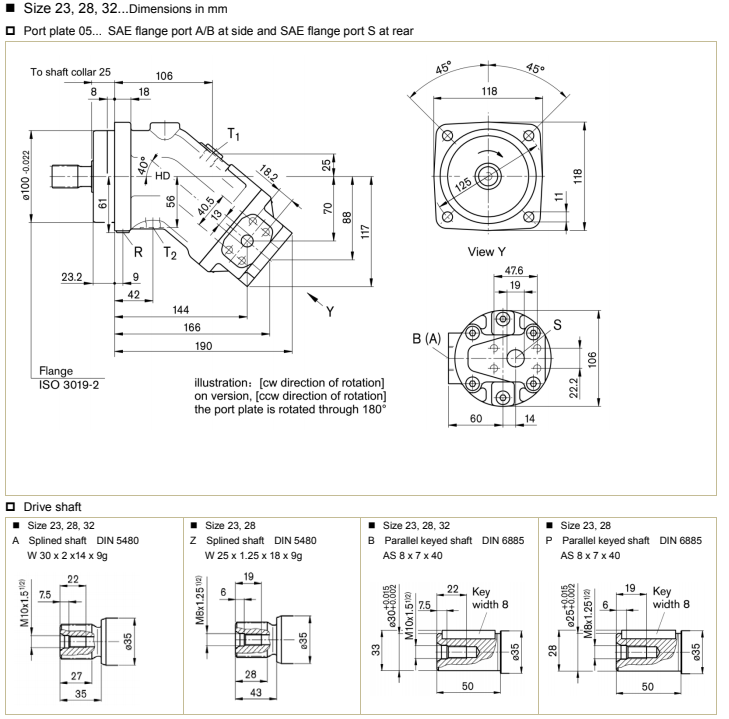
Ports | Port for | Standard | Size 2) | P Max [bar] 3) | State 7) |
B(A) | Working port Fastening thread | SAE J518 5) DIN13 | 1/2” M8 x 1.25 deep 15 | 450 | O |
S | Suction port Fastening thread | SAE J518 5) DIN13 | 3/4” M10 x 1.5 deep 17 | 30 | O |
T 1, T 2 | Drain port | DIN 3852 4) | M16 x 1.5 deep 12 | 3 | O/X 6) |
R | Air bieed | DIN 3852 4) | M10 x 1 deep 12 | 3 | X |
Note
1) Center bore according to DIN 332 (thread according to DIN 13)
2) For the maximum tightening torques the general instructions must be observed .
3) Momentary pressure spikes may occur depending on the application. Keep this in mind when selecting measuring devices and fittings.
4) The spot face can be deeper than specified in the appropriate standard
5) Only dimensions according to SAE J518, metric fastening thread is a deviation from standard.
6) Depending on the installation position, T1 or T2 must be connected
7) O = Must be connected (plugged on delivery) X = plugged (in normal operation)
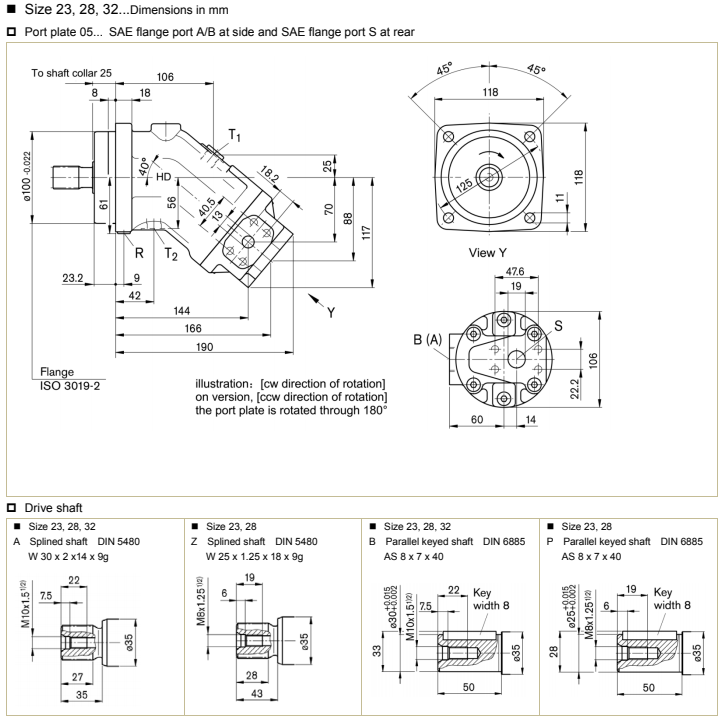
Ports | Port for | Standard | Size 2) | P Max [bar] 3) | State 7) |
B(A) | Working port Fastening thread | SAE J518 5) DIN13 | 3/4” M10 x 1.5 deep 17 | 450 | O |
S | Suction port Fastening thread | SAE J518 5) DIN13 | 1” M10 x 1.5 deep 17 | 30 | O |
T 1, T 2 | Drain port | DIN 3852 4) | M18 x 1.5 deep 12 | 3 | O/X 6) |
R | Air bieed | DIN 3852 4) | M12 x 1.5 deep 12 | 3 | X |
Note
1) Center bore according to DIN 332 (thread according to DIN 13)
2) For the maximum tightening torques the general instructions must be observed .
3) Momentary pressure spikes may occur depending on the application. Keep this in mind when selecting measuring devices and fittings.
4) The spot face can be deeper than specified in the appropriate standard
5) Only dimensions according to SAE J518, metric fastening thread is a deviation from standard.
6) Depending on the installation position, T1 or T2 must be connected
7) O = Must be connected (plugged on delivery) X = plugged (in normal operation)
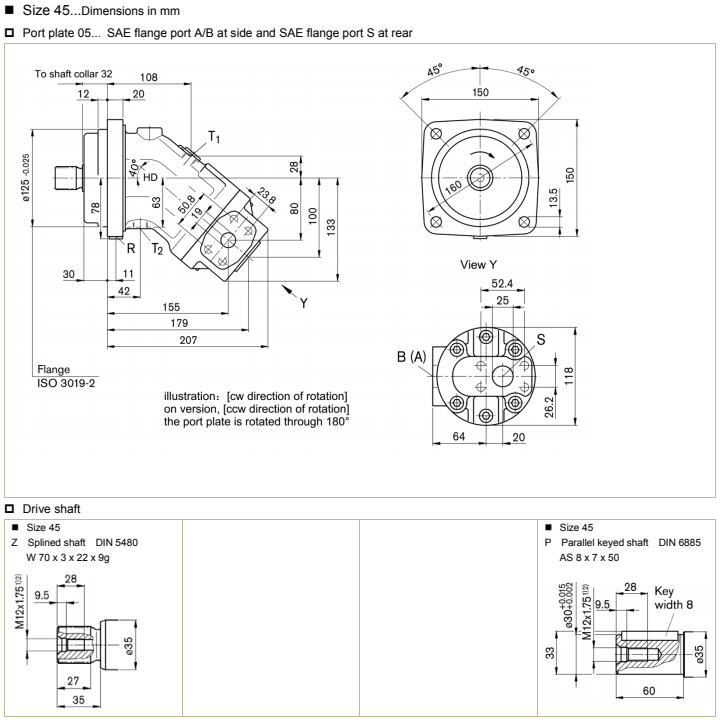
Ports | Port for | Standard | Size 2) | P Max [bar] 3) | State 7) |
B(A) | Working port Fastening thread | SAE J518 5) DIN13 | 3/4” M10 x 1.5 deep 17 | 450 | O |
S | Suction port Fastening thread | SAE J518 5) DIN13 | 1” M10 x 1.5 deep 17 | 30 | O |
T 1, T 2 | Drain port | DIN 3852 4) | M18 x 1.5 deep 12 | 3 | O/X 6) |
R | Air bieed | DIN 3852 4) | M12 x 1.5 deep 12 | 3 | X |
Note
1) Center bore according to DIN 332 (thread according to DIN 13)
2) For the maximum tightening torques the general instructions must be observed .
3) Momentary pressure spikes may occur depending on the application. Keep this in mind when selecting measuring devices and fittings.
4) The spot face can be deeper than specified in the appropriate standard
5) Only dimensions according to SAE J518, metric fastening thread is a deviation from standard.
6) Depending on the installation position, T1 or T2 must be connected
7) O = Must be connected (plugged on delivery) X = plugged (in normal operation)
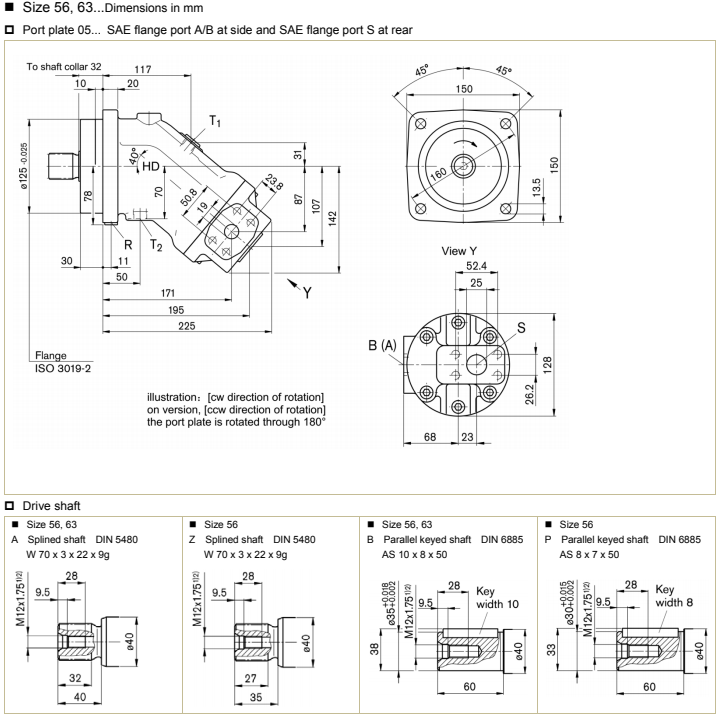
Ports | Port for | Standard | Size 2) | P Max [bar] 3) | State 7) |
B(A) | Working port Fastening thread | SAE J518 5) DIN13 | 3/4” M10 x 1.5 deep 17 | 450 | O |
S | Suction port Fastening thread | SAE J518 5) DIN13 | 1” M10 x 1.5 deep 17 | 30 | O |
T 1, T 2 | Drain port | DIN 3852 4) | M18 x 1.5 deep 12 | 3 | O/X 6) |
R | Air bieed | DIN 3852 4) | M12 x 1.5 deep 12 | 3 | X |
Note
1) Center bore according to DIN 332 (thread according to DIN 13)
2) For the maximum tightening torques the general instructions must be observed .
3) Momentary pressure spikes may occur depending on the application. Keep this in mind when selecting measuring devices and fittings.
4) The spot face can be deeper than specified in the appropriate standard
5) Only dimensions according to SAE J518, metric fastening thread is a deviation from standard.
6) Depending on the installation position, T1 or T2 must be connected
7) O = Must be connected (plugged on delivery) X = plugged (in normal operation)
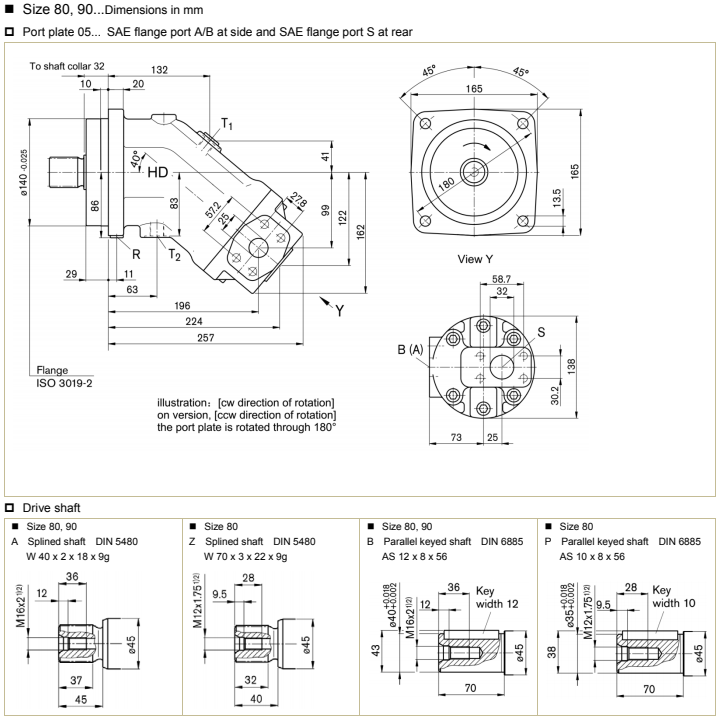
Ports | Port for | Standard | Size 2) | P Max [bar] 3) | State 7) |
B(A) | Working port Fastening thread | SAE J518 5) DIN13 | 1” M12 x 1.5 deep 17 | 450 | O |
S | Suction port Fastening thread | SAE J518 5) DIN13 | 1- 1/4” M10 x 1.5 deep 17 | 30 | O |
T 1, T 2 | Drain port | DIN 3852 4) | M18 x 1.5 deep 12 | 3 | O/X 6) |
R | Air bieed | DIN 3852 4) | M12 x 1.5 deep 12 | 3 | X |
Note
1) Center bore according to DIN 332 (thread according to DIN 13)
2)For the maximum tightening torques the general instructions must be observed
3) Momentary pressure spikes may occur depending on the application. Keep this in mind when selecting measuring devices and fittings.
4) The spot face can be deeper than specified in the appropriate standard
5) Only dimensions according to SAE J518, metric fastening thread is a deviation from standard.
6) Depending on the installation position, T1 or T2 must be connected
7) O = Must be connected (plugged on delivery) X = plugged (in normal operation)
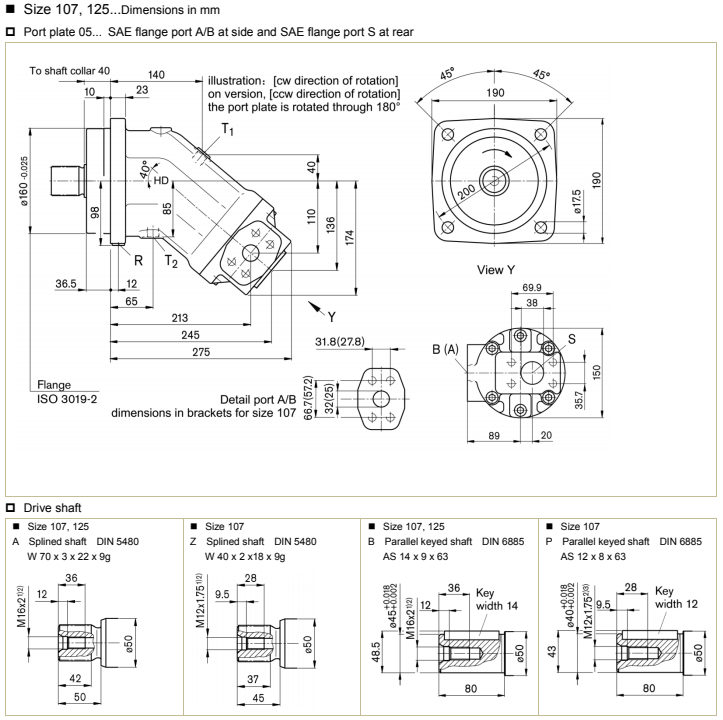
Ports | Port for | Standard | Size 2) | P Max [bar] 3) | State 7) |
B(A) Size 107 | Working port Fastening thread | SAE J518 5) DIN13 | 1” M12 x 1.75 deep 17 | 450 | O |
B(A) Size 125 | Working port Fastening thread | SAE J518 5) DIN13 | 1- 1/4” M14 x 2 deep 19 | 450 | O |
S | Suction port Fastening thread | SAE J518 5) DIN13 | 1- 1/2” M12 x 1.75 deep 20 | 30 | O |
T 1, T 2 | Drain port | DIN 3852 4) | M18 x 1.5 deep 12 | 3 | O/X 6) |
R | Air bieed | DIN 3852 4) | M14 x 1.5 deep 12 | 3 | X |
Note
1) Center bore according to DIN 332 (thread according to DIN 13)
2) For the maximum tightening torques the general instructions must be observed .
3) Momentary pressure spikes may occur depending on the application. Keep this in mind when selecting measuring devices and fittings.
4) The spot face can be deeper than specified in the appropriate standard
5) Only dimensions according to SAE J518, metric fastening thread is a deviation from standard.
6) Depending on the installation position, T1 or T2 must be connected
7) O = Must be connected (plugged on delivery) X = plugged (in normal operation)
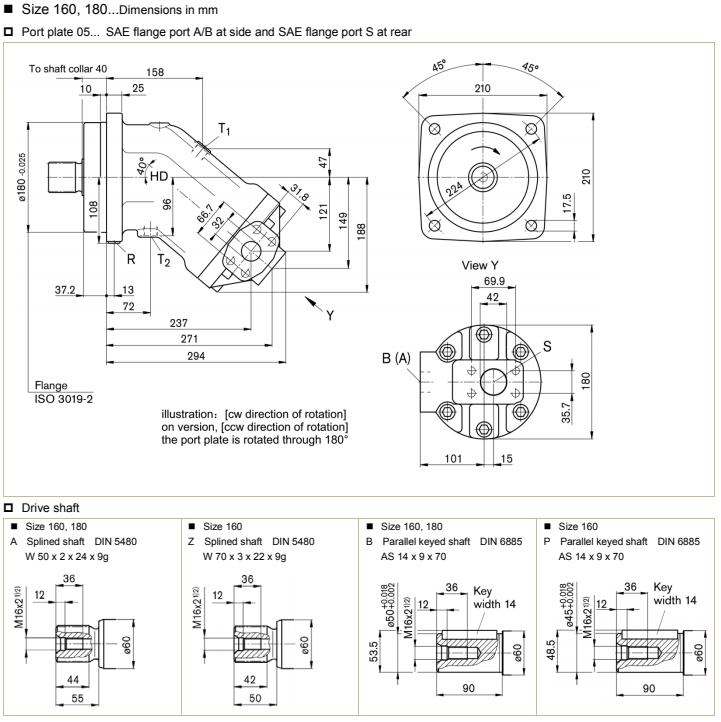
Ports | Port for | Standard | Size 2) | P Max [bar] 3) | State 7) |
B(A) | Working port Fastening thread | SAE J518 5) DIN13 | 1- 1/4” M14 x 2 deep 19 | 450 | O |
S | Suction port Fastening thread | SAE J518 5) DIN13 | 1- 1/2” M12 x 1.75 deep 20 | 30 | O |
T 1, T 2 | Drain port | DIN 3852 4) | M22 x 1.5 deep 14 | 3 | O/X 6) |
R | Air bieed | DIN 3852 4) | M14 x 1.5 deep 12 | 3 | X |
Note
1) Center bore according to DIN 332 (thread according to DIN 13)
2) For the maximum tightening torques the general instructions must be observed .
3) Momentary pressure spikes may occur depending on the application. Keep this in mind when selecting measuring devices and fittings.
4) The spot face can be deeper than specified in the appropriate standard
5) Only dimensions according to SAE J518, metric fastening thread is a deviation from standard.
6) Depending on the installation position, T1 or T2 must be connected
7) O = Must be connected (plugged on delivery) X = plugged (in normal operation)
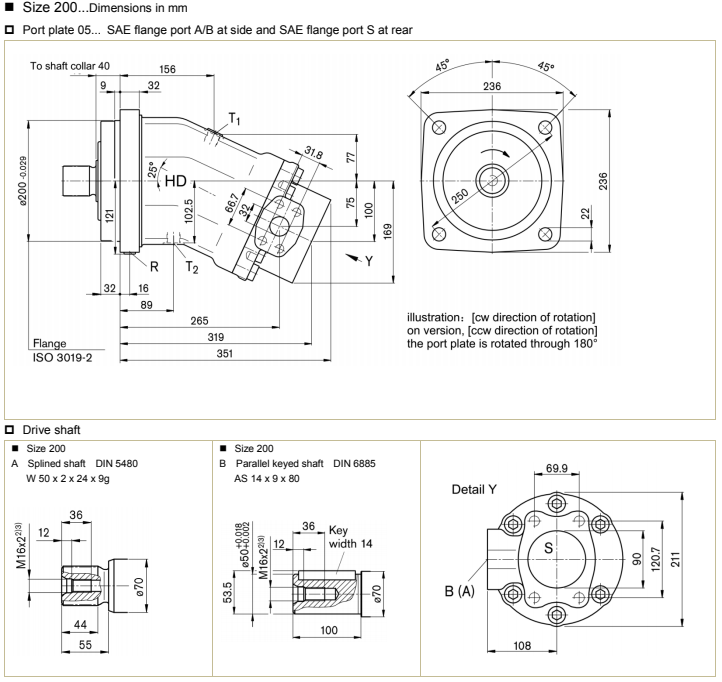
Ports | Port for | Standard | Size 3) | P Max [bar] 1) | State 7) |
B(A) | Working port Fastening thread | SAE J518 5) DIN13 | 1- 1/4” M14 x 2 deep 19 | 450 | O |
S | Suction port Fastening thread | SAE J518 5) DIN13 | 3- 1/2” M16 x 2 deep 24 | 30 | O |
T 1, T 2 | Drain port | DIN 3852 4) | M22 x 1.5 deep 14 | 3 | O/X 6) |
R | Air bieed | DIN 3852 4) | M14 x 1.5 deep 12 | 3 | X |
Note
1) Momentary pressure spikes may occur depending on the application. Keep this in mind when selecting measuring devices and fittings.
2) Center bore according to DIN 332 (thread according to DIN 13)
3) For the maximum tightening torques the general instructions must be observed .
4) The spot face can be deeper than specified in the appropriate standard
5) Only dimensions according to SAE J518, metric fastening thread is a deviation from standard.
6) Depending on the installation position, T1 or T2 must be connected
7) O = Must be connected (plugged on delivery) X = plugged (in normal operation)
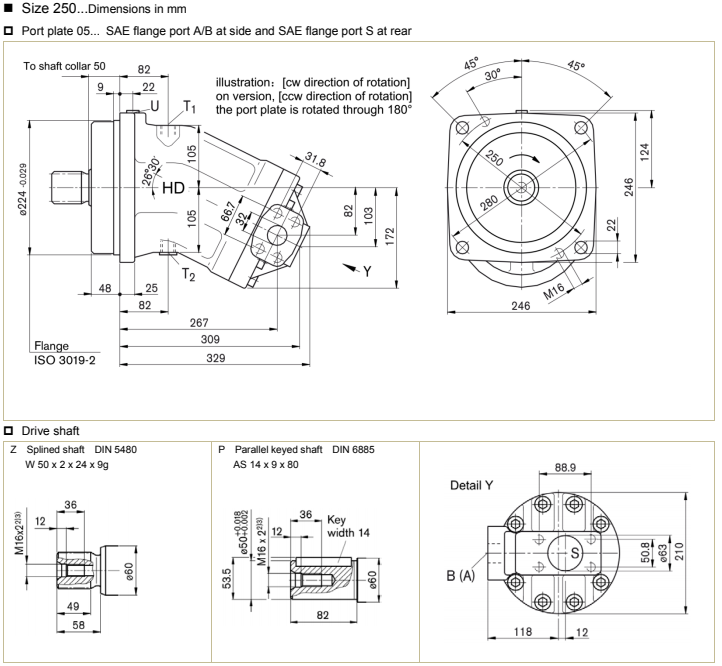
Ports | Port for | Standard | Size 3) | P Max [bar] 1) | State 7) |
B(A) | Working port Fastening thread | SAE J518 5) DIN13 | 1- 1/4” M14 x 2 deep 19 | 400 | O |
S | Suction port Fastening thread | SAE J518 5) DIN13 | 2- 1/2” M12 x 1.75 deep 17 | 30 | O |
T 1, T 2 | Drain port | DIN 3852 4) | M22 x 1.5 deep 14 | 3 | X/O 6) |
U | Air bieed | DIN 3852 4) | M14 x 1.5 deep 12 | 3 | X |
Note
1) Momentary pressure spikes may occur depending on the application. Keep this in mind when selecting measuring devices and fittings.
2) Center bore according to DIN 332 (thread according to DIN 13)
3) For the maximum tightening torques the general instructions must be observed .
4) The spot face can be deeper than specified in the appropriate standard
5) Only dimensions according to SAE J518, metric fastening thread is a deviation from standard.
6) Depending on the installation position, T1 or T2 must be connected
7) O = Must be connected (plugged on delivery) X = plugged (in normal operation)
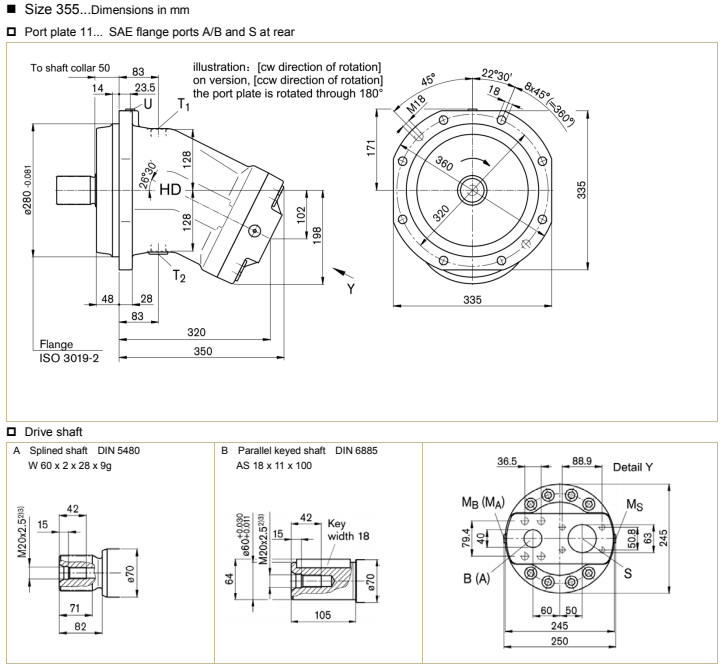
Ports | Port for | Standard | Size 3) | P Max [bar] 1) | State 7) |
B(A) | Working port Fastening thread | SAE J518 5) DIN13 | 1- 1/2” M16 x 2 deep 21 | 400 | O |
S | Suction port Fastening thread | SAE J518 5) DIN13 | 2- 1/2” M12 x 1.75 deep 17 | 30 | O |
T 1, T 2 | Drain port | DIN 3852 4) | M33 x 2 deep 18 | 3 | O/X 6) |
U | Bearing flushing port | DIN 3852 4) | M14 x 1.5 deep 12 | 3 | X |
M A, MB | Measuring workting pressure | DIN 3852 4) | M14 x 1.5 deep 12 | 400 | X |
M S | Measuring suction pressure | DIN 3852 4) | M14 x 1.5 deep 12 | 30 | X |
Note
1) Momentary pressure spikes may occur depending on the application. Keep this in mind when selecting measuring devices and fittings.
2) Center bore according to DIN 332 (thread according to DIN 13)
3) For the maximum tightening torques the general instructions must be observed .
4) The spot face can be deeper than specified in the appropriate standard
5) Only dimensions according to SAE J518, metric fastening thread is a deviation from standard.
6) Depending on the installation position, T1 or T2 must be connected
7) O = Must be connected (plugged on delivery) X = plugged (in normal operation)
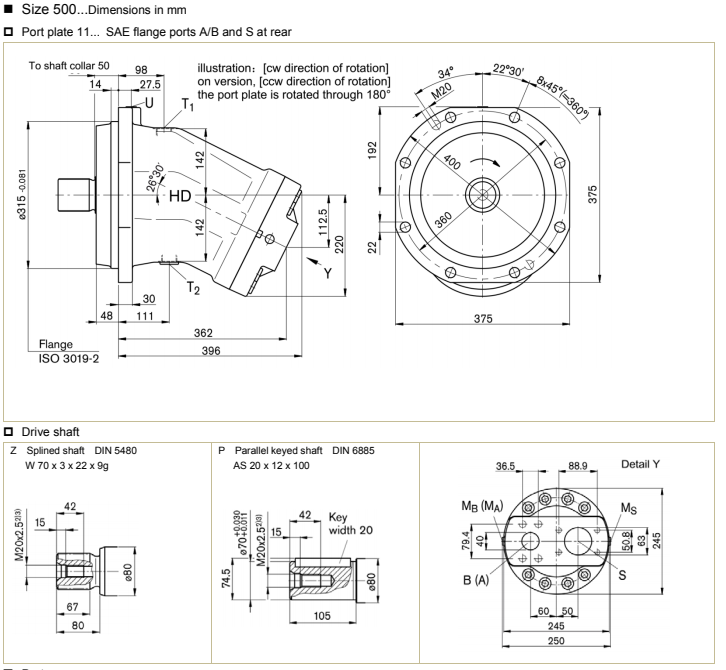
Ports | Port for | Standard | Size 3) | P Max [bar] 1) | State 7) |
B(A) | Working port Fastening thread | SAE J518 5) DIN13 | 1- 1/2” M16 x 2 deep 21 | 400 | O |
S | Suction port Fastening thread | SAE J518 5) DIN13 | 3” M16 x 2 deep 24 | 30 | O |
T 1, T 2 | Drain port | DIN 3852 4) | M33 x 2 deep 18 | 3 | O/X 6) |
U | Bearing flushing port | DIN 3852 4) | M18 x 1.5 deep 12 | 3 | X |
M A, M B | Measuring workting pressure | DIN 3852 4) | M14 x 1.5 deep 12 | 400 | X |
M S | Measuring suction pressure | DIN 3852 4) | M14 x 1.5 deep 12 | 30 | X |
Note
1) Momentary pressure spikes may occur depending on the application. Keep this in mind when selecting measuring devices and fittings.
2) Center bore according to DIN 332 (thread according to DIN 13)
3) For the maximum tightening torques the general instructions must be observed .
4) The spot face can be deeper than specified in the appropriate standard
5) Only dimensions according to SAE J518, metric fastening thread is a deviation from standard.
6) Depending on the installation position, T1 or T2 must be connected
7) O = Must be connected (plugged on delivery) X = plugged (in normal operation)
HD-A2FO Axial Piston Fixed Pump Installation instructions
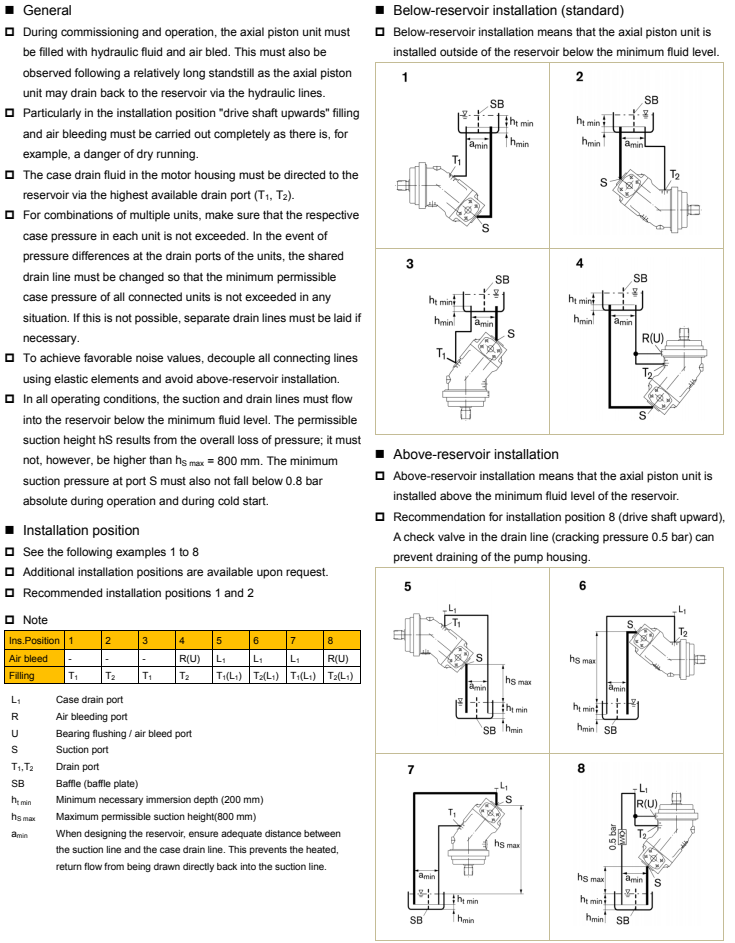
Technical Information
Hydraulic fluid
Before starting project planning, please refer to our data sheets mineral oil and environmentally acceptable hydraulic fluids for detailed information regarding the choice of hydraulic fluid and application conditions.
When using environmentally acceptable hydraulic fluids, the limitations regarding technical data and seals must be observed.
Please contact us. When ordering, indicate the hydraulic fluid that is to be used.
Notes on the choice of hydraulic fluid
In order to select the correct hydraulic fluid, it is necessary to know the operating temperature in the reservoir (open circuit) in relation to the ambient temperature.
The hydraulic fluid should be selected so that within the operating temperature range, the viscosity lies within the optimum range (nopt), see shaded section of the selection diagram. We recommend to select the higher viscosity grade in each case.
Example: at an ambient temperature of X ℃ the operating temperature is 60℃. In the optimum operating viscosity range (Vopt; shaded area) this corresponds to viscosity grades VG 46 resp. VG 68; VG 68 should be selected.
Important
The case drain temperature is influenced by pressure and input speed and is always higher than the reservoir temperature.
However, at no point in the component may the temperature exceed 90℃. The temperature difference specified on the left is to be taken into account when determining the viscosity in the bearing
If the above conditions cannot be met, due to extreme operating parameters please contact us.
Filtration of the hydraulic fluid
The finer the filtration the better the cleanliness level of the hydraulic fluid and the longer the service life of the axial piston unit.
In order to guarantee the functional reliability of the axial piston unit it is necessary to carry out a gravimetric evaluation of the hydraulic fluid to determine the particle contamination and the cleanliness level according to ISO 4406.
A cleanliness level of at least 20/18/15 must be maintained.
At very high hydraulic fluid temperatures (90℃ to maximum 115℃), a cleanliness level of at least 19/17/14 according to ISO 4406 is necessary.
If the above cleanliness levels cannot be maintained, contact us.
Viscosity and temperature of hydraulic fluids
Viscosity | Shaft seal | Temperature 3) | Comment | |
Cold start | Vmax ≤1600 mm2/s | NBR 2) FKM | θSt ≥ -40℃ θSt ≥ -25℃ | t ≤3 min, without load (P ≤ 50 bar) n≤1000 rpm Permissible temperature difference between axial piston unit and hydraulic fluid in the system maximum 25 K |
Warm-up phase | V = 1600~400 mm2/s | t ≤15 min,P ≤0.7*P nom and n ≤ 0.5*n nom | ||
Continuous operation | V = 400~10 mm2/s1) | NBR 2) FKM | θ= +85℃ T = +110℃ | measured at port L, L1 |
V = 36~16 mm2/s | Range of optimum operating viscosity and efciency | |||
Short-term operation | V = 10~7 mm2/s | NBR 2) FKM | θ = +85℃ θ = +110℃ | t ≤3 min,P ≤0.3*P nom measured at port L, L1 |
1)Corresponds e.g. for VG 46 to a temperature range of +4 °C to +85 °C (see selection diagram)
2)Version EA10VSO...-P (if operating with HFA, HFB and HFC hydraulic fluids)
3)If the temperature at extreme operating parameters cannot be adhered to, please contact us
Selection diagram
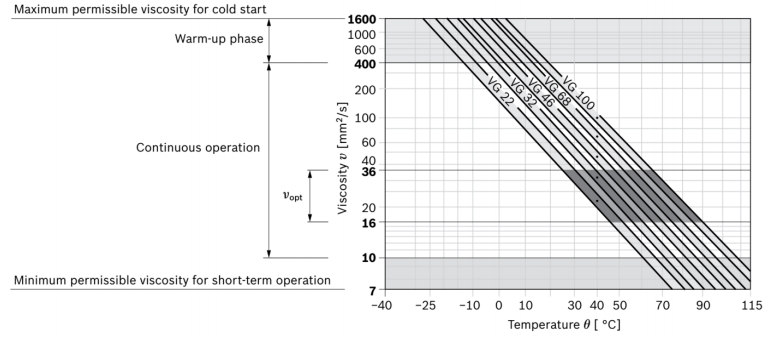
General instructions
The pump HD-A2FO is designed to be used in open circuits. The motor HD-A2FM/E is designed to be used in open and closedcircuits.
The project planning, installation and commissioning of the axial piston unit requires the involvement of qualified personnel.
Before using the axial piston unit, please read the corresponding instruction manual completely and thoroughly.
During and shortly after operation, there is a risk of burns on the axial piston unit. Take appropriate safety measures (e.g. by wearing protective clothing).
Depending on the operating conditions of the axial piston unit (operating pressure, fluid temperature), the characteristic may shift.
Service line ports
The ports and fastening threads are designed for the specified maximum pressure.
The machine or system manufacturer must ensure that the connecting elements and lines correspond to the specified application conditions (pressure, flow, hydraulic fluid, temperature) with the necessary safety factors.
The service line ports and function ports can only be used to accommodate hydraulic lines.
The data and notes contained herein must be adhered to.
The product is not approved as a component for the safety concept of a general machine according to ISO 13849.
The following tightening torques apply
Fittings
Observe the manufacturer's instructions regarding tightening torques of the fittings used
Mounting bolts
For mounting bolts with metric ISO thread according to DIN 13 or with thread according to ASME B1.1, we recommend checking the tightening torque in individual cases in accordance with VDI 2230.
Female threads in the axial piston unit
The maximum permissible tightening torques MG max are maximum values for the female threads and must not be exceeded. For values, see the following table.
Threaded plugs
For the metallic threaded plugs supplied with the axial piston unit, the required tightening torques of threaded plugs MV apply. For values, see the following table.
Ports | Maximum permissible tightening torque of the female threads M Gmax | Required tightening torque of the threaded plugs Mv1) | hexagon socket in the threaded plugs WAF | |
Standard | Size of thread | |||
DIN 3852 | M8 x 1 | 10 Nm | 7 Nm | 3 mm |
M10 x 1 | 30 Nm | 12 Nm | 5 mm | |
M12 x 1.5 | 50 Nm | 25 Nm 2) | 6 mm | |
M14 x 1.5 | 80 Nm | 35 Nm | 6 mm | |
M16 x 1.5 | 100 Nm | 50 Nm | 8 mm | |
M18 x 1.5 | 140 Nm | 60 Nm | 8 mm | |
M22 x 1.5 | 210 Nm | 80 Nm | 10 mm | |
M26 x 1.5 | 230 Nm | 120 Nm | 12 mm | |
M27 x 2 | 330 Nm | 135 Nm | 12 mm | |
M33 x 2 | 540 Nm | 225 Nm | 17 mm | |
M42 x 2 | 720 Nm | 360 Nm | 22 mm | |
DIN ISO 228 | G1/4” | 40 Nm | - | - |
Note
1) The tightening torques apply for screws in the "dry" state as received on delivery and in the "lightly oiled" state for installation.
2) In the "lightly oiled" state, the MV is reduced to 10 Nm for M10 x 1 and 17 Nm for M12 x 1.5.